About us
JAXA Aviation helps to create a safer and more prosperous society with aeronautics-related research and development activities.
FLIGHT PATH No.23 | 2019 SUMMER
<People>
Realizing a numerical simulation environment for engine developers to compete at the world’s top level
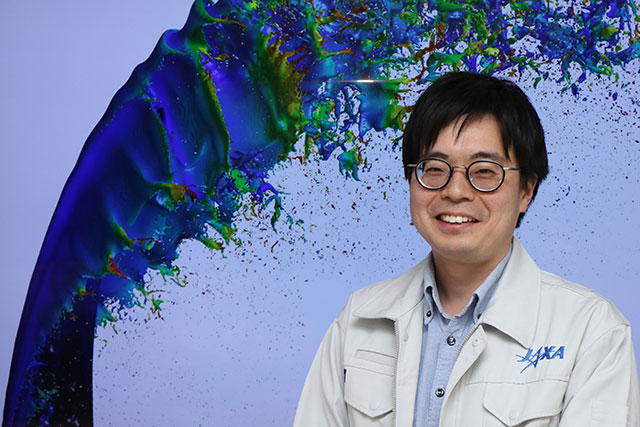
NAMBU Taisuke
Researcher
Combustion and Turbulence Section
Numerical Simulation Research Unit
Photo:In front of a visualized image of liquid fuel injected from an engine combustor nozzle
Can you tell us about your current research?
I am currently studying numerical simulation technologies that deal with combustion and turbulence phenomena inside aircraft engines. More specifically, I focus on simulating the liquid fuel atomization processes. Fuel injected from an engine combustor nozzle breaks into small particles. The size of fuel particles has a considerable impact on the evaporation speed of fuel. Therefore, it is extremely important to predict the particle size and spatial distribution of injected fuel in achieving an ideal combustion, yet a lot remains unknown around this phenomenon. In particular, it is difficult to take measurements around fuel injection nozzles in an experiment, so it is desired that simulation clarify the phenomenon. However, this phenomenon is very challenging to simulate because it is a very fine phenomenon and involves multiple phases.
I was also a member of the Innovative Combustion Technology Project for the government’s Cross-ministerial Strategic Innovation Promotion Program (SIP). In this project, I contributed to the development of the core program for automotive engine simulation software called “HINOCA.” This software uses numerical simulation technologies employed in JAXA’s aircraft and rocket research. Researchers in the automotive industry are required to produce analysis results in a very limited amount of time. It involves different kinds of difficulties than scientific numerical simulations. Through much trial and error, we developed low-cost simulation software that minimizes the cost of mesh generation, which is the most costly part of traditional methods.
What made you want to join JAXA?
In my fourth year at college, I joined an aerospace laboratory, and I had an opportunity to study the wall interference of wind tunnels as a technical trainee at JAXA. This experience was the decisive factor. A wind tunnel has walls, and the impact of the walls from the measurement results has to be deduced in order to accurately reproduce the actual state of an aircraft in flight. At JAXA, they were comparing the results of numerical simulation with and without the walls to clarify the impact of the walls. The target wind tunnel had porous walls, and it was assumed that this affected test results considerably. My first task was to create a numerical model of the porous walls. When we conducted a simulation test using the new porous wall model, the results perfectly matched the measurements of an actual wind tunnel test with the walls. It was a wonderful experience. I really enjoyed the whole experience, and I later wrote my doctoral thesis on this research.
What is your next goal?
In developing aircraft engines, if you could spend as much time and money as you needed, you could make many prototypes to test new ideas. However, both budget and time are limited. That’s why numerical simulation plays an important role in the early stages of development. The development process will be efficient if you can make a rough estimate through simulation before starting detailed design. However, simulation of an aircraft engine is far from mature, and it still has a long way to go to be commonly used in actual development. One of my goals is to provide the world’s most sophisticated engine simulation environments to Japanese engine manufacturers competing on the global stage. I frequently discuss with JAXA’s young researchers the future of aircraft engine research and development.
There is still room for improvement with HINOCA. I want to improve HINOCA to make it more user friendly and contribute to the Japanese automotive research field.
Do you have any advice for those aspiring to join the Aviation Technology Directorate?
At JAXA, and especially the Aviation Technology Directorate, new hires are expected to contribute from the first year, but the culture here allows researchers to conduct research freely. Of course, requirements of our organization are not easy to meet, but I am satisfied with the current environment. JAXA has a supercomputer leading numerical simulation research in Japan, and it is an attractive environment for numerical simulation researchers.
Interviewee: NAMBU Taisuke, Researcher, Combustion and Turbulence Section, Numerical Simulation Research Unit
Born in 1987. NAMBU completed a doctoral program at Waseda University School of Fundamental Science and Engineering in October 2014, and joined JAXA in 2015 after completing postdoctoral research at the Japan Society for the Promotion of Science. He engaged in the research of wind tunnel wall interference using numerical simulation at university. He has been engaged in the research of numerical simulation technology for combustors since joining JAXA.