Research & Development
JAXA promotes three research and development programs and a fundamental research program that underpins them.
Combustion simulation technologies
To enable the frontloading of combustor design processes, we are developing numerical simulation technologies that deal with combustion and turbulent phenomena inside aircraft engine. We are working to unravel and model the complex flow phenomena in a jet engine combustor, and develop CFD software for combustion simulations using the developed models.
Detailed simulation of fuel primary atomization
We are developing models for fuel primary atomization using detailed numerical simulations.
To enable the accurate simulation of flow fields inside a combustor, it is necessary to provide accurate values of size and spatial distributions of injected fuel particles, as these distributions have a considerable impact on engine combustor efficiency. However, it is difficult to measure details of the fuel primary atomization around the nozzles, and therefore the fuel particle size and spatial distributions can only be inferred with conventional models. This uncertainty is one of the bottlenecks of combustor simulations.
In this study, we are simulating the details of the fuel primary atomization and developing a model to simulate particle size and distribution of fuel primary atomization. The model is applied to simulate entire flow-field inside a combustor.
In the future, we plan to conduct simulations that incorporate the processes of vaporization of atomized fuel, mixing it with air and burning the mixture to understand the detailed physical phenomena of spray combustion and construct a spray combustion model.
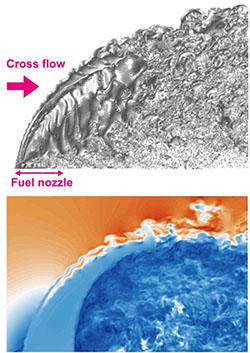
Visualization of the liquid phase surface and velocity distribution near a fuel injector nozzle
Direct numerical simulation of turbulent boundary layers accompanied by separation and reattachment
Turbulent boundary layer separation is one of the most challenging issues in the aerospace field. The separation phenomena can be categorized into “geometrical separation” like backward-facing step flow and “separation caused by an adverse pressure gradient” as seen in the flow over a wing surface. This study involves direct numerical simulation (DNS) of turbulent boundary layers accompanied by separation and reattachment caused by pressure bubbles that alter the pressure gradient. We also plan to move forward with DNS data analysis and the development of turbulence models using DNS data.
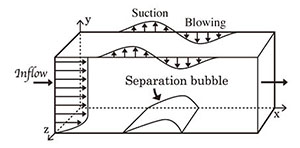
Flow configuration
Flow separation and reattachment are induced by applying blowing and suction at the upper boundary of the computation domain. This yields a separation bubble (recirculation region). One of the characteristics of this flow field is the spatiotemporal changes in separation and reattachment lines. For the inflow data, the DNS data of a zero-pressure-gradient turbulent boundary layer is given.
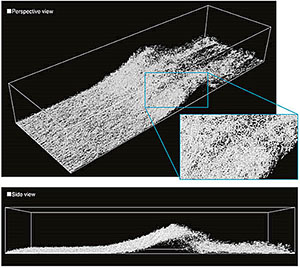
Isosurfaces of a vortex structure / Positive value of the second invariant of the fluctuating velocity tensor (direction of flow is from the lower left to the upper right)
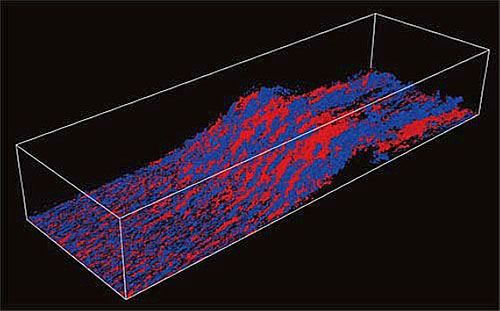
Isosurface of streamwise velocity fluctuations (Reθ = 1500) / Red: high speed; Blue: low speed (direction of flow is from the lower left to the upper right)
Development of engine combustion simulation software
JAXA had been participating in the Innovative Combustion Technology Project (FY2014–FY2018) under the Cabinet Office’s Cross-ministerial Strategic Innovation Promotion Program (SIP). Through the project, we developed a 3D CFD core-software of automotive engine combustion simulation called HINOCA. The most distinctive feature of the HINOCA is that combustion flow simulation can be run directly from the engine cylinder configuration data. There is almost no need to perform mesh generation, which used to take weeks or even months.
Currently, we are working to rebuild the software HINOCA to simulate combustion phenomena inside aeroengines, which have different mechanisms of combustion from those of automotive engines. We are going to develop the sub-models for atomization, turbulence, spray combustion, etc., to build an aeroengine combustion simulation software that can be used in combustor design processes.
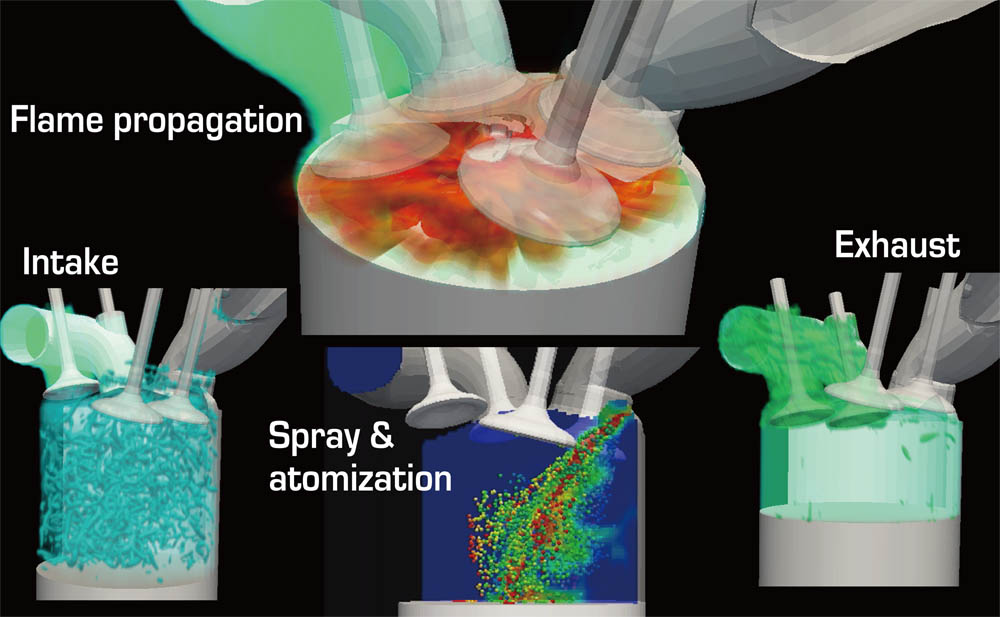
Simulation of the whole combustion cycle of an automotive engine (intake, spray and atomization, flame propagation, exhaust)
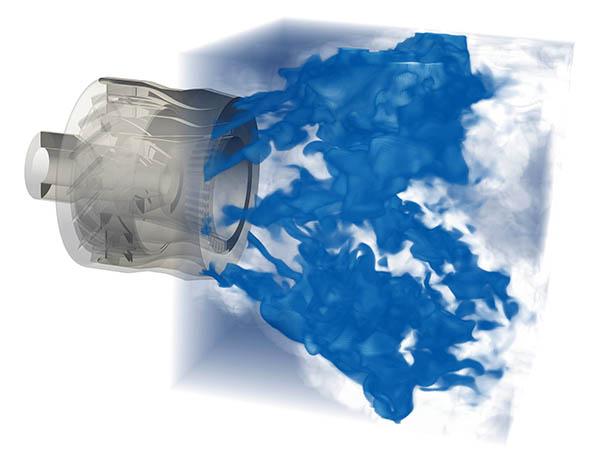
Vaporized fuel flow from a jet engine single injector simulated by HINOCA
March 30, 2020