About us
JAXA Aviation helps to create a safer and more prosperous society with aeronautics-related research and development activities.
FLIGHT PATH No.23 | 2019 SUMMER
<Advanced research into composite materials and structures>
Thermoplastic CFRP, a promising next-generation aircraft material
In the current circumstances where the cost reduction of aircraft is required, thermoplastic CFRP is now highlighted as a next-generation aircraft material to replace thermosetting CFRP. TAKEDA Shin-ichi introduces the current progress and future scope of JAXA’s research in this field.

TAKEDA Shin-ichi
Associate Senior Researcher
Structures and Advanced Composite Research Unit
Spotlight returns to thermoplastic CFRP
Tell us about JAXA’s research on thermoplastic CFRP
Thermosetting carbon fiber reinforced plastic (CFRP) is being used for the primary structure of aircraft. Thermosetting CFRP becomes hard when heated and never resumes the original softness. The cost reduction of thermosetting CFRP is not easy because its process and related-facilities are expensive and already matured technology. Since the cost reduction is now highly demanded for aircraft production, thermoplastic CFRP, which is widely used in the automobile industry, has emerged as a new technology. It uses resin that softens when heated and hardens when cooled.
About 30 years ago, JAXA did the study of thermoplastic composites when it was still called National Aerospace Laboratory (NAL) and found some advantageous points. Take a type of thermoplastic CFRP using polyether-ether-ether-ketone (PEEK) resin for example, it is highly resistant to impact and therefore very unlikely to get damaged. It is superior to thermosetting CFRP as an aircraft material. Thermoplastic CFRP allows various molding methods. Secondary processing of the substance is easy. While thermosetting CFRP requires storage in a freezer or other low-temperature environments, thermoplastic CFRP doesn’t and is better in terms of storage costs. However, it needs to be molded in higher temperatures than thermosetting CFRP. So, it costs a lot of money for production equipment. That is the reason the application to aircraft has been delayed. In recent years, technological advancements including the improvement of material properties and the lowering of molding temperatures made thermoplastic CFRP gain attention again. The use as a secondary structural material has also begun. Airbus A380 has employed it in the leading edge of its main wings.
How do you plan to advance the research of thermoplastic CFRP?
Our current challenge is to enhance the potentials and applicability of thermoplastic CFRP as a primary structural material. As a requirement for its research and development, JAXA first focuses on analysis of damage tolerance. In order to adopt a new material as a primary structural material for aircraft, it is necessary to mature its properties including safety. Thermoplastic CFRP is stronger than thermosetting CFRP because it is soft and easily dents to release impacts. We need to study this mechanism further intensively. It may be also necessary to change the method for detecting damages of parts when impacted if a new material is employed. For that purpose, we need to analyze and consider the characteristics of materials.
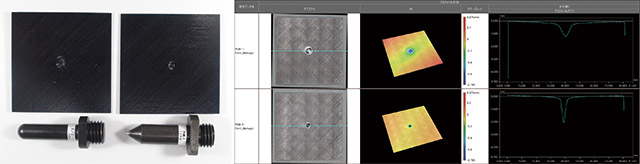
Impact damage test in which objects of different shapes collided against a plate of thermoplastic CFRP at the same speed. Properties and structural design of composite parts are determined based on the difference in damage that occurs inside the composite plate.
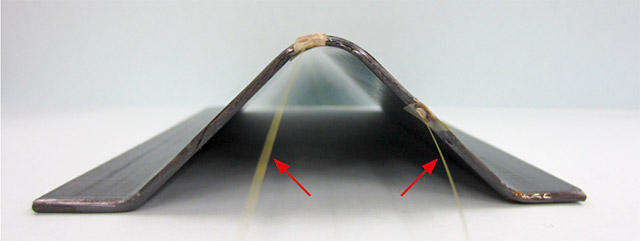
Thermoplastic CFRP specimen heated and then bended by press forming. Optical fiber sensor (shown with arrow) is embedded to investigate internal strain that occurs at the moment material deforms.
Pursuing bonding technology unique to Japan
What do you think is a key for thermoplastic CFRP to be widely used?
The development of bonding technology is also important for the manufacturing of large aircraft components. In the case of thermosetting CFRP, thermosetting adhesive films are sandwiched between parts and reheated to bond them. In the case of thermoplastic CFRP, however, the boundary faces of parts are welded into one. When Airbus and other makers fabricate secondary structures, they employed a method that they embedded materials that generate heat by electromagnetic induction in parts and formed them and then heated the materials from outside with a high frequency magnetic field. However, this method has drawbacks that the heat generating material would possibly affect the strength and the heating consumes a huge amount of electricity.
So, we focused our attention on ultrasonic welding that is used in the production of automobiles and medical supplies. It uses ultrasonic wave to heat and weld bonding surfaces while applying pressure on them. With this bonding process, the problems that electromagnetic induction welding has can be solved in principle. We achieved a strength comparable to that of thermosetting film adhesive bonding in fundamental testing we have done so far. Although the difficulty still remains in applying to large structures, we think the key to the spread of thermoplastic CFRP is ultrasonic welding.
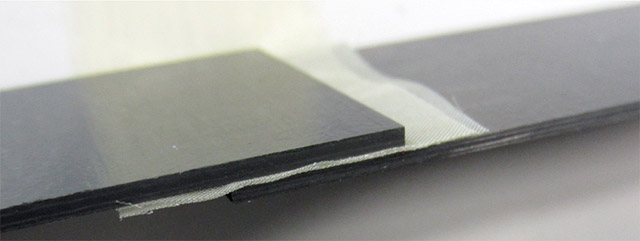
Ultrasonic welding of PEEK/ CFRP coupon. Two plates of composite material are welded with a resin mesh sheet placed between them.
Is ultrasonic welding under research in other countries?
Researchers in Europe and the United States are also working on it. However, JAXA takes an approach slightly different from those of them. In JAXA’s method, we insert sheet-shaped resin between parts to bond them. This method stably provides high strength. In addition, it has technological compatibility since it has common points with those methods used for thermosetting CFRP. So, we think it will be easily implemented. We are also trying to develop a new technology to expand bonded area without compromising quality.
How do you plan to advance your research in the future?
Though thermoplastic CFRP is a challenging subject and has a lot of difficulties, it is very promising as a next-generation aircraft material. Its problem is still total cost. We expect that the material could help Japan’s aviation industry enhance its international competitiveness if the overall cost reduction is achieved throughout its manufacturing process. We need to understand the details of its impact resistance mechanism that the material softly dents and reduces internal damages, improve bonding technology including ultrasonic welding that will be the key of its spread, and standardize the material and test methods in order to reduce costs. We have to achieve the three tasks in a simultaneous and parallel way. In the future, thermoplastic CFRP will integrate with automation that has been highly advanced for thermosetting materials. It is our important mission to suggest and demonstrate such technologies.
Feature Story
Advanced research into composite materials and structures