Research & Development
JAXA promotes three research and development programs and a fundamental research program that underpins them.
Scarf sanding technology for carbon fiber reinforced plastics (CFRP) airframe
Summary of the page
- When composite aircraft experiences damage by lighting, hail, and so on, the damaged area has needed to be repaired manually by technical experts. However, because of the expanding demand for aircraft, there is likely to be a shortage of this technical expertise in the near future.
- JAXA, in collaboration with Shinmei Industry Co., Ltd., and Shinmei Tohoku Machinery Co., Ltd., is developing a device that can automatically perform the scarf sanding work, a process of scarf repair to sand down several plies in the CFRP laminate around the damaged area depending on the degree of damages.
- This page introduces the scarf repair process applied to repair CFRP airframe together with the background and co-developer’s voice.
The CFRP repair work requires highly technical skills and in-depth knowledge on the properties of the materials. These works are usually performed manually, requiring a significant amount of time. Therefore, JAXA has been studying the way to make the most of such expertise into automated technology. This has led to the development of the Automated Scarf Sanding Device.
A footage from a demonstration test in January 2022. (3:30)
(For subtitles in English, click gear icon in the lower right corner to access the video settings menu, then click on "Subtitles" and "English".)
Why CFRP repair technology?
Carbon fiber reinforced plastics (CFRP) have the advantage of being lighter in weight than metal materials, which is ideal for use in aircrafts’ structural materials. With recent aircraft, the ratio of composites in the structural weight is increasing, with some containing 50 percent of the structural weight, and the number of aircraft applying composite airframe are expected to continue to increase due to the growing demand for further weight reduction. Aircraft are susceptible to damage from lightning strikes, hail, stones that are kicked up from runway surfaces, tools that are accidentally dropped during routine maintenance and repairs, and so on. In particular, winter lighting, while rare globally, is more common on the coast of the Sea of Japan, and there have been numerous cases that composite airframe got damaged due to lightning strikes. While such damage does not always affect the flight immediately, if cracks are left unattended, they could expand and cause severe accidents. For that reason, if small cracks of several centimeters are found on airframes, inspection and repair are conducted.
The benefit of automating CFRP repair
JAXA has been engaged in research on automated scarf sanding technology to reduce labor and time burdens for the scarf sanding process of CFRP repair work. This is because the importance of CFRP repair technology is growing rapidly as the heavy maintenance of composite aircraft will begin in the 2020s. The standard method for CFRP repair work is, first, to check the crack’s width, depth and degree using NDT (Nondestructive Testing); next, the damaged area is sanded down into a mortar shape. Then, it is layered with repair materials and joined together with adhesive film.
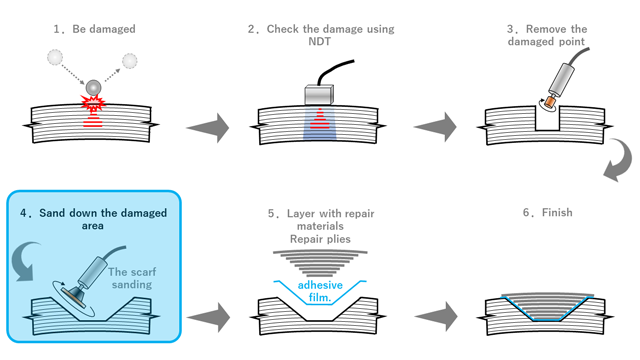
The work of scarf repair includes sanding down the damaged area into a conical shape. The scarf sanding process takes approximately 120 minutes for the technical expert working in facing downward position, and for novice technician, this work can take 480 minutes (300 minutes on average). If this scarf sanding process can be automated, anyone can perform the scarf sanding work without having expert technical skills in a short amount of time, as few as 100 minutes. Such automation can reduce the time required to do this work by 67 percent, and it is not always necessary to use people to do the work.
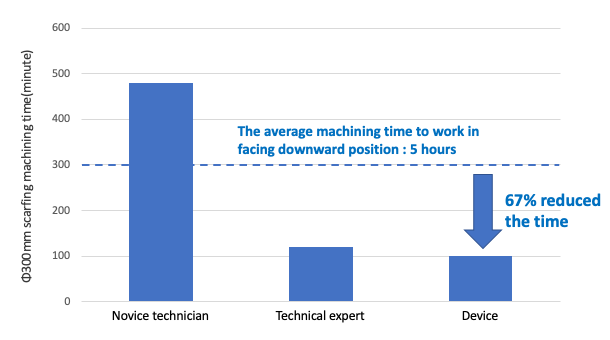
An Automated Scarf Sanding Device
-
The developed "CFRP Automated Scarf Sanding Device" set up on a composite airframe.
- JAXA has been working with Shinmei Industry Co., Ltd., and Shinmei Tohoku Machinery Co., Ltd., to develop an Automated Scarf Sanding Device which applies JAXA’s automated scarf sanding technology. This development is an outcome of the open innovation scheme named “JAXA Aeronautics Innovation Challenge 2016.”
The device is attached to the composite airframe with ten “legs” and conducts the scarf sanding automatically. The digital machining shape data entry and programming are not necessary to do this work. Now, we are improving the device’s performance based on users’ feedback, such as decreasing the weight of the device body (from 67 kg to 40 kg), reducing the amount of time required to perform the repair work, and increasing the durability of the cut and shaped area. Our plans are underway to make practical use of this device in 2021.
Voices of collaborators on an Automated Scarf Sanding Device
We visited Shinmei Industry Company’s Chokoji Plant (located in the city of Toyota in Aichi Prefecture) and heard about their challenges and thoughts on the CFRP Automated Scarf Sanding Device. You can find how the device works from the following footage.
Bringing easy to carry and easy to use devices to the world
The Automated Scarf Sanding Device is 65 cm in diameter, 50 cm in height, and weighs 67 kg, equivalent to two small truck tires, and can be carried by two or three workers. Because the device is kept in place on the airframe by suction cups on the tips of ten legs, the device can easily be installed even upside down under the body of the aircraft and can be attached onto vertical tail structures.
During the development of this device, we considered how to make professional repairs without manpower or large amounts of time; we focused on the sanding down(scarfing) process and designed the device with handling and safety foremost in our minds. As a result, the device setup is a non-covered configuration like the one shown in this photograph, and it is designed to have a simple mechanical structure using general gears and cams. We used lightweight and strong CFRP for the components in order to reduce the device’s weight; in this way, the device is portable and convenient like other handheld tools.

The device legs are kept in place on the airframe along the fuselage form.
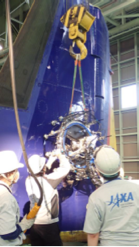
The device is lightweight, it can be attached onto vertical tail structures.
As the device can provide the same or more accurate finishing quality as the scarf sanding by hands, the existing certification processes should apply and additional examinations for aircraft safety are not necessary. These features would also help ease and lower the burden of introduction of this device, providing benefits for airlines and MROs (Maintenance Repair Overhaul companies).
PRESIDENT KAZUHIKO SASAKI (at the time)
Shinmei Industry Co., Ltd., has a 70-year history of contributing to manufacturing automated production equipments for automotive companies. They have been accumulating their own technology, experience, and know-how, along with GFRP (glass fiber reinforced plastic) machining, for over 30 years. Making the most of these technologies, they have been engaging in a challenging project to develop an automated scarf repair device for CFRP airframe in collaboration with JAXA. The company’s president, Sasaki Kazuhiko, talks about the continuing trend of support for the company with greater potential in Aichi Prefecture. It was natural for the company to enter the aviation field from a different industry.
Shinmei Tohoku Machinery Co., Ltd., as a member of Shinmei Industry, has taken charge of the processing technology. Sugayama Katsumi, the company president, looked back at how difficult it was to enter the field of aviation from a different industry, as aviation and CFRP were unknown territories at the beginning of the development. He stated, “We did not have the knowledge concerned with the effects on the electronic components and the composite materials in and around the aircraft repair. Therefore, we often groped in the dark, for example, to build the water- cooling equipment at the sanding process which is ill-suited for aircraft maintenance.
Shiroyama Yoshitaka, from Shinmei Industry Co., Ltd. (General Manager, Technical Division, Development Department) expects the device to undergo further improvements and to be available on the market in the future. He said, “Currently, the automated device can be activated only at the sanding process. We will keep doing our best to reach our goal of having the entire composite repair processes automated in the future.”
PRESIDENT KATSUMI SUGAYAMA
DEPUTY DIVISION MANAGER TECHINICAL PLANNING DEPT. YOSHITAKA SHIROYAMA
A young engineer, Shimizu Hideyuki (Technical Division, Development Department), stated, “I believe that we are doing the development that no other company is offering, and it will lead to the next step up in my career.” Another young engineer (Technical Division, Development Department), Hoshiya Eisuke, added, “I am still learning product development by trial and error every day. I will work to find a solution to the challenge for the exhibition at the International Paris Airshow that will be held in 2021.”
ASSISTANT MANAGER TECHINICAL PLANNING DEPT. HIDEYUKI SHIMIZU
ENGINEER TECHINICAL PLANNING DEPT. EISUKE HOSHIYA
Hikaru Hoshi, Structures and Advanced Composite Research Unit, Aviation Technology Directorate, JAXA, who has been addressing research on composite repair technology for over 15 years since 2003, has been working on this collaborative research from its beginning and expects the device to go on the market in the future. He attended the test of the device installation onto the vertical tail of the YS-11.
Since the days as the National Aerospace Laboratory of Japan (NAL), a predecessor, JAXA has been accumulating expertise on composite materials together with evaluation technology. The R&D outputs are then passed over to the private sector companies for development of practical products etc. The collaboration on the development of an Automated Scarf Sanding Device is a great example of open innovation; based on the fertile soil of composites that JAXA has been cultivating over the years, we saw the seeds of CFRP repair technology and watering them with an open innovation framework “JAXA Aeronautics Innovation Challenge,” which brought a private sector company having different expertise in automotive industry to work on automation technology in the aviation field, and eventually came to a fruition of Automated Scarf Sanding Device.
The people involved in this development gather around the device.
March 31, 2020