CFRP損傷修復スカーフサンディング工法 PURPO
本ページの概要
- 航空機に使われるようになった複合材料が、雷や雹などによって損傷した場合、熟練した専門家の手作業が必要になります。
- しかし、近い将来航空機の需要拡大などによって、専門家の人手不足が予想されています。
- JAXAでは、機体の修復作業を機械化する装置を、新明工業株式会社・新明東北マシナリー株式会社と共同で開発中です。
- このページでは、複合材料の修復技術を解説するとともに、共同開発者に装置開発にかけた想いを語ってもらいました。
炭素繊維強化プラスチック(CFRP)は、金属材料に比べて軽いという利点から航空機の構造材として優秀であるため、現在では機体重量の50%以上にCFRPを使用した機種も登場しています。今後、航空機の需要は増加すると予測されており、それに伴ってCFRPを採用した機体も増えていくと考えられます。航空機は、落雷や雹、滑走路上で跳ねた小石、整備中の工具落下などによって破損する場合があります。特に日本では、世界的にも珍しい冬季雷(冬の雷)が日本海側で発生するため、航空機が被雷し損傷を受けるケースも少なくありません。損傷が直ちに飛行に支障を及ぼすわけではありませんが、そのまま放置すれば亀裂が拡大し、大きな事故につながる可能性もあります。そのため、数cm程度の損傷が発生した場合でも、検査や修理が行われています。CFRPの修復には専門家が必要であり、また修復作業にも時間がかかります。JAXAでは、熟練した技能がなくても、短い時間でCFRPの修復を行うための研究とその技術を応用した「自動スカーフサンディング装置」の開発を行っています。
PURPO取付試験(3分30秒)
2022年1月に三菱航空機株式会社の機体で実施した取付試験の映像です。PURPOの特徴について星主任研究開発員が説明しております。
CFRP修復技術
2020年頃からは、CFRPを多用した機体の徹底的な検査・整備を行う重整備が始まります。重整備では、損傷個所は必ず補修・修復しなければならず、CFRP修復技術の重要性は高まっています。一般的なCFRP修復の手順としては、まず傷の大きさや深さなど損傷の度合いを非破壊試験(NDT: Nondestructive Testing)で調べ、ダメージを受けた部分を削り取ります。さらにその場所をすり鉢状に削り取った後、損傷箇所と同じように修理材を積み重ねた後にフィルム状の接着剤で張り合わせます。
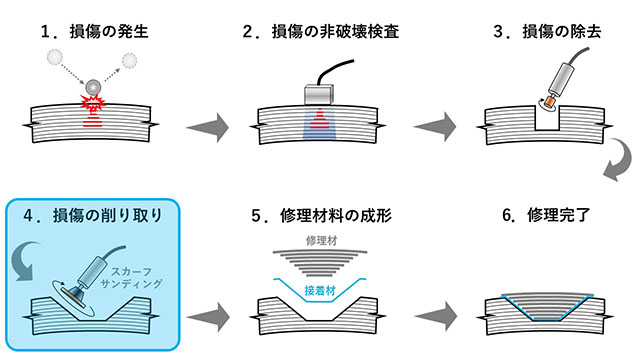
CFRP修復の流れ
損傷箇所をすり鉢状に削る(スカーフサンディング)作業は、下向きで作業を行う場合で1カ所につき、熟練した技術者で120分、初級技術者で480分(平均して300分)程度必要とされています。
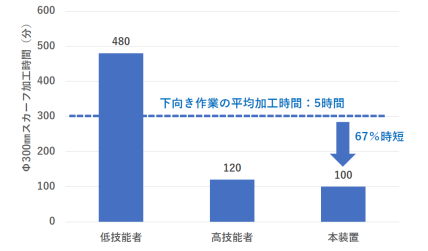
加工時間の比較(下向き作業の場合)
JAXAでは、CFRP修復におけるスカーフサンディング工程の人的および時間的負担を削減すべく、自動スカーフサンディング技術の研究に取り組んできました。自動化できれば、技術の習熟度に関係なく、およそ100分という短い作業時間で誰でもがスカーフサンディングを行うことが可能となります。自動化によって、およそ67%も作業時間を短縮できるうえ、常に人員を配置して作業する必要もありません。
自動スカーフサンディング装置
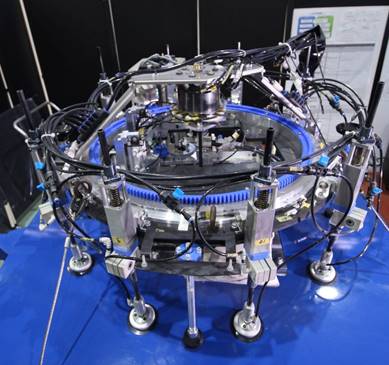
航空機を模した構造物の上での試験の様子
今回、JAXAの自動スカーフサンディング技術を応用した「自動スカーフサンディング装置」を新明工業株式会社とともに開発しました。これは平成28年度「JAXA航空技術イノベーションチャレンジ」の成果の一つです。
装置は、10本の脚で機体に吸着し、自動的にスカーフサンディングを行います。加工形状のデータ入力やプログラミングの必要はありません。
現在、本体重量の軽量化(67kg→40kg)や作業時間の短縮、切削部分の耐久性向上など、ユーザーから寄せられた意見を元に改良を行っており、2021年の実用化を目指しています。
プロジェクト名称
本装置の開発プロジェクト名称がPolymer matorix composite Ultimate Repair PrOject。通称、PURPO(プルポ)に決定しました。八本足の吸盤機構からスペイン語でタコ意味するPulpoに着想を得た名称となります。
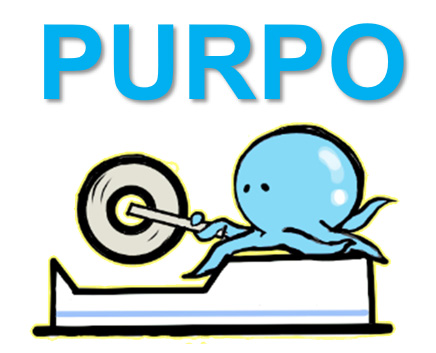
Polymer matorix composite Ultimate Repair PrOject
〜新明工業株式会社に聞くCFRP自動スカーフサンディング装置の共同研究〜
JAXAとの共同研究により装置開発を進める、新明工業株式会社長興寺工場(愛知県豊田市)を訪ね、実際にCFRP自動スカーフサンディング装置が動くところを見せてもらいながらお話を聞きました。
持ち運びがしやすく使い勝手の良い「道具や工具」のような装置を世の中へ
縦横幅65cm、高さ50cmで重量約67kgの自動スカーフサンディング装置は、小型トラックのタイヤを二つ重ねたぐらいのサイズで、作業員が2~3名いれば持ち運びができます。航空機の機体には10本脚の先端にある吸盤で固定するので、胴体の下面に逆さまに設置したり、垂直尾翼に張り付くように設置することも可能です。
開発の際は、熟練した技術者のような修復の仕上がりを、人員や時間をかけずに実現するにはどうしたらよいかを考え、「削る」という工程に絞って、取り回しのしやすさや安全の確保などを突き詰めて設計しました。その結果、装置は写真のようにむき出しの構造になりました。また、ごく一般的な歯車などで構成するシンプルな「からくり構造」を目指したといいます。装置の部品にも軽くて丈夫なCFRPを使用することにより、さらに軽量化を図りました。こうして、大がかりな修復装置でなく、持ち運びがしやすく使い勝手の良い「道具や工具」のような装置が出来上がったのです。
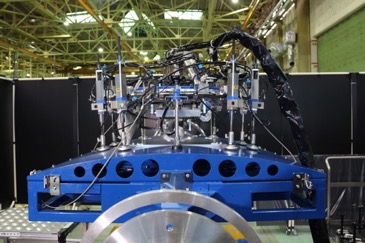
機体の形状に沿って脚を固定する
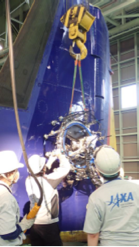
軽量なので垂直尾翼へも設置可能
この装置を使えば、現在行われている複合材修復と同等の加工状態(仕上がり)を提供できるので、既存の認証体系をそのまま利用でき、機体の安全性に関する追加の審査は不要です。エアラインにとっても負担が少なく、導入しやすいというメリットがあります。
共同研究開発を行った新明工業株式会社とJAXA航空技術部門が目指すもの
新明工業株式会社は、もともと自動車メーカーの製造設備などへの貢献で70年の経験と実績をもつ会社です。そして、液晶などに用いられるGFRP(ガラス繊維強化プラスチック)を加工する事業に30年以上携わってきた知見や技術を活かして、JAXAとの共同研究で航空分野のCFRP修理技術を獲得するというチャレンジングな事業に取り組みました。 同社取締役社長の佐々木和彦氏によれば、愛知県には企業のポテンシャルを活かした事業展開を後押しする機運があり、「異分野から航空分野へ新規参入することは自然な流れでした」と言います。 |
![]() 新明工業株式会社 取締役社長 |
|
加工技術を担当するのは、新明工業のグループ会社である新明東北マシナリー株式会社です。社長の菅山勝美氏は、航空分野にもCFRPにも未知だった開発当初は、「修理部の周囲に存在する電子部品や複合材への影響が出ることを知らず、削る工程で水を使う装置を作るなどいつも手探りだった」と、異分野から航空分野に参入する難しさを振り返ります。 装置をさらに改良して市販化を目指す新明工業の城山吉隆氏(テクニカル本部 開発部部長)は、「装置が自動化するのはまだ削る工程だけです。これからさらに突き詰めて、将来は全工程を自動化したい」と将来への期待を語ります。 |
![]() 新明東北マシナリー株式会社 社長 |
![]() 新明工業株式会社 テクニカル本部開発部部長 |
若手開発者の志水秀行氏(テクニカル本部 開発部 開発室)は、「他社ではやっていない開発を自分たちがやれるのは、自分の経験にもつながる」と話し、同じく星屋瑛祐氏(テクニカル本部 開発部 開発室)も、「日々トライ&エラーで商品づくりの勉強中。2020年のファンボロ―国際国空ショーでの発表に向けて課題を解決してきたい」と話してくれました。 |
![]() 新明工業株式会社 テクニカル本部開発部開発室 |
![]() 新明工業株式会社 テクニカル本部開発部開発室 |
JAXA航空技術部門 構造・複合材技術研究ユニットの星光主任研究開発員は、2003年以来、もう15年以上もCFRP修復の研究を進めています。この共同研究にも立ち上げから関わっており、将来の市場投入を想定してYS-11の垂直尾翼に直接装置を取り付けた試験にも立ち会いました。 航空宇宙技術研究所(NAL)時代から培ってきたJAXAの評価技術、複合材への知見と、それを受けて企業が開発が進めるという関係。日本にある優れた技術を用いた自動スカーフサンディング装置という種が、JAXA航空技術イノベーションチャレンジ公募をきっかけに芽を出し、この共同研究を通じて育まれていく一つの事例となっています。 |
||
![]() 装置を囲む開発関係者(左より城山氏、星氏、菅山氏、佐々木氏、星屋氏、志水氏) |